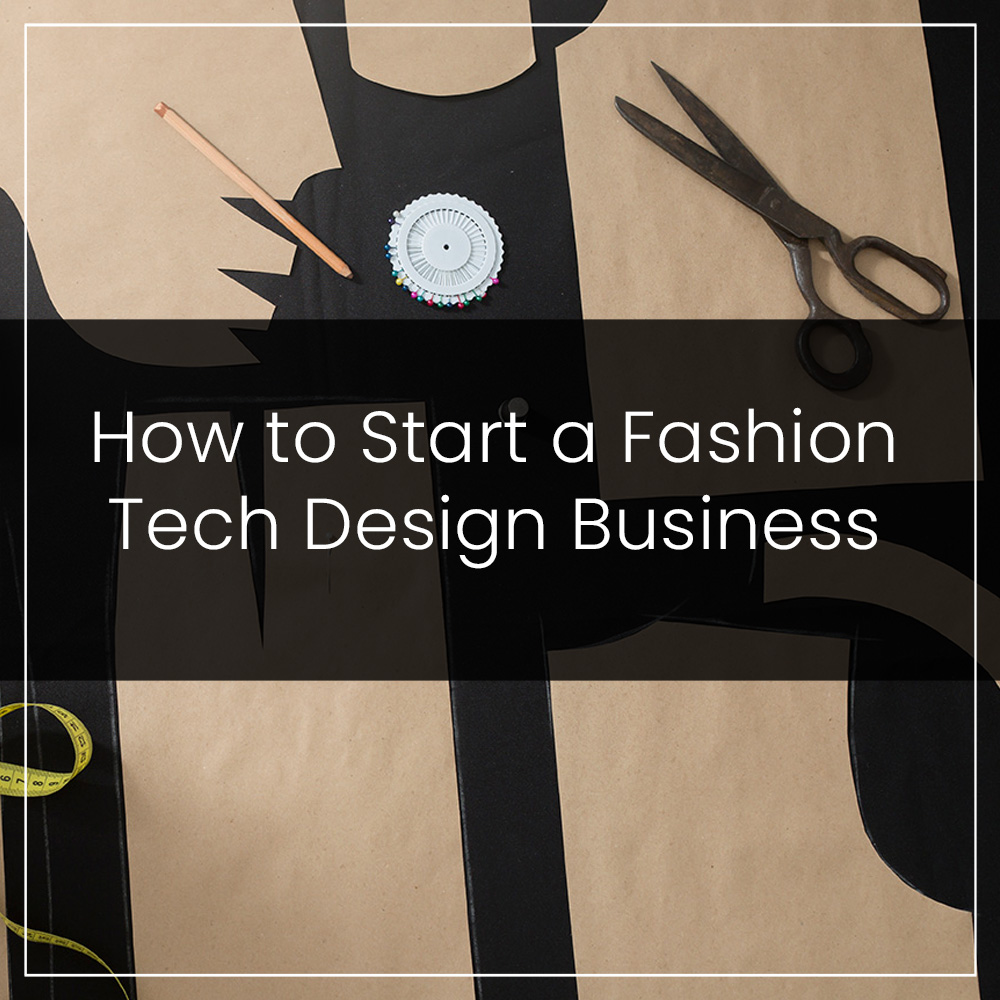
Welcome to the “Designers, Plans, and Coffee Podcast,” where we explore the multifaceted world of fashion. In this episode, we take a fascinating journey with LaTisha Winston, the founder of Keeping You in Stitches, a company specializing in technical design for the fashion industry. LaTisha’s unique story showcases the diversity of opportunities within fashion and the critical role of quality control.
Discover how LaTisha’s fashion journey began with a twist. Her dream-inspired company name, “Keeping You in Stitches,” embodies her passion and commitment to the fashion industry.
Explore the world of technical design, pattern-making, and quality control as we delve into LaTisha’s expertise. She shares her experiences working with a wide range of clients, from corporate companies to independent designers and individuals seeking to learn the art of sewing and pattern-making.
Learn about the importance of quality control in the fashion industry, from visiting factories overseas to washing your new clothing before wearing it. LaTisha’s insights highlight the significance of ensuring the integrity of garments and the role of those who make fashion magic happen behind the scenes.
For those aspiring to enter the fashion industry, LaTisha offers valuable advice on the importance of learning pattern-making and sewing. Embrace her journey from struggling with drawing to becoming a prominent figure in the fashion world.
As technology continues to shape the industry, LaTisha discusses the rise of 3D tech design and avatars, offering exciting opportunities for remote work in fashion.
Join us for an inspiring and insightful conversation.
Links mentioned:
I was learning how to draw and all I saw was white people. I remember showing it to one of my aunties in the community. She was like, This person doesn’t look like you. Why are you drawing white people? From then on, I was like, Everybody I’m drawing is black. I’m sorry.
Welcome to the Designers, Plans and Coffee Podcast, where we discuss how to succeed as a designer while staying true to yourself, finding peace in the process, and making money doing what we love. Subscribe on YouTube and wherever you get your podcasts.
Today, we’re going to get into how Tish started her company and the lessons learned and how you can start your own. Tish, take it away.
I started my business, actually, I was consulting and doing a lot of freelancing when I moved back home to Maryland. I also was doing some refashioning, repurposing, and alterations. I didn’t actually have a name for the company. It actually came to me in a dream because I kept saying, Well, what’s the name of the company? Keeping stitches. Okay, well, that’s nice, but what’s the name of the company? It’s like I was having a conversation.
I’m like, Keeping you in stitches. Right. Then I woke up and was like, Oh, okay.
Look at that. That’s the name of the company.
That is how the name came about. How I actually got started, as I said, I was in Maryland, and in Maryland, there were not a lot of corporate companies besides Under Armor, hey UA. Once I left there, I actually began to freelance for a tennis wear company. I did that majority of the time while I was in Maryland. With that, also getting my business set up as an LLC and making sure it was registered in Maryland, that’s how I actually began to do the business. I also was a mentor for, well, actually, I’m still a part of the fashion incubator in DC with Macy’s. I do a lot of mentoring and teaching on product development. I did a couple of classes for that. That’s how when I realized like, Oh, Is the teacher. I do know a lot and this information is not known to everyone because it comes to me so easily.
And that’s especially true with teaching because you’re like, but this is basic things. And then you’re like, Well, I guess it’s not so basic.
Exactly. Because you’ve been learning over a couple of years. I mean, how long have you been doing this? And then people are just starting. It’s like, What do you mean you don’t know this? Oh, no. Yes. Start from the beginning.
It’s second nature to me, not you.
Exactly. Yes, that’s it. It’s second nature to me. And just telling and mentoring and seeing a lot of designers that did not go to school and the pitfalls that they will fall into of just something basic as you sent all of your samples where? Overseas. Have you ever been over there? Do you know this factory? No. Why would you do that? That’s why it didn’t come back. It probably wasn’t a factory. Something like that.
Really, to me came so easy. I’m like, Why would you do that? No.
Right. Now, keeping you in stitches, who do you serve and what do you do?
For them? I serve corporate, and when I say corporate, meaning I do technical design. That is if you’ve ever tried on a garment and it did not fit, hello, technical design. That’s what we do. We are the people who make sure your garment fits right, it’s hanging properly, also that it actually holds up to the standards, whatever the company has decided. I am that tech fit expert. I do that with a lot of corporate companies, starting with new brands, new labels and private labels. I do teach fashion education for, as I said before, those who did not go to school, I teach them on the side and also mentor independent designers, and I am also an educator. I am a college professor. I went back to school to get my master’s for that. So a lot of blood, sweat, and tears. I say that because if you all go back to the first episode I told you about what happened in undergrad and how my grades were not great. Actually, this reminded me that I didn’t actually get kicked out. They put me on academic probation and my mother got mad and pulled me out.
So it was like.
You got kicked out.
Yeah, it was like I got kicked out.
She got kicked out, but not by the school. The school didn’t kick you out. Your mother kicked you out.
I had to prove that I was serious about it, so I had to come home for two years. Then I tried to make sure I went back and finish. So that is who Keeping You in Stitches serves. It serves the corporate all the way down to the independent designer. People who just want to learn to sew. They want to learn pattern making, every type of stitch from the stitch that you could use to make an invisible wig is the same stitch that you use for embroidered thread.
How did you know that technical design was your calling and that was going to be your area of expertise?
Remember when I said first episode that I went to textile because I could not draw? Well, it did not get better after the first year. I hated some of those drawing classes. I was like, I can’t do this.
I will reveal your dirty little secret here. I did Tisha’s drawings. I don’t even know if you knew that, Zahiyya.
I had no idea.
I did all of Tisha’s drawings for her. She would tell me what she wanted it to look like, and I would draw them for her. So part of that degree is mine.
It’s funny because when I went to grad school completely online, they had us drawing so many sketches where I actually started getting cramps in my hand in carpal tunnel and was wearing a brace while I’m trying to do all these sketches. And then I actually hired someone to help me sketch better because I was like, This will not defeat me. I need to know how to do this if I’m going to be an educator.
My question is, what type of sketches? Are you talking about fashion sketches? Or you’re talking about flat sketches?
We were doing illustrations. I was bringing her designs to life on paper. Okay. So she wanted this design for a crop tank top. I don’t remember the top. I just remember she wanted to sketch for these ostrich feather pants. I’m going to reveal another trade secret. Ms. Zahiyya made us black girl croquies and they have hips and they have boobs. And so I put these ostrich feather pants. And I think it was purple. She loves purples. I think it was purple and red and navy. I sketched it out for her, and then I put the color in, and I’m pretty sure she got an A.
I did.
Because I knew her.
Nowadays, do you have to know how to sketch? Because right now all you have to do is know how to do flat sketching for technical design.
It’s funny because I can do flat sketching. I have no problem with that.
You just can’t do the fashion illustration.
I couldn’t get the nine heads right.
I don’t know. And I can’t do flat sketching. I can do the nine heads. I can do all the body poses. I can do all of that. I can put the detail in the garment. But that flat sketching and that technical and making those slopers, nooo.
The nine head thing, it’s not really like the average person. That’s like a model that’s six something. That’s why I was so adamant about doing black girl croquies because it’s like, we don’t look like that. We have hips. We have… Well, I don’t have a lot of boobs, but I have boobs. You want to show stuff that’s going to look good on you. So you have to draw like the black girl’s croquies. It’s funny because when I was growing up and I was learning how to sketch anyway, it’s like back story. I was learning how to draw, and all I saw was white people. I remember showing her to one of my aunties in the community, she past away, but she was one of my mentors, and she was one of the people who taught me how to sew. She was like, This person doesn’t look like you. She’s like, This person doesn’t look like you, why are you drawing white people? From then on, I was like, Everybody I’m drawing is black. I’m sorry.
But that’s what we grew up on, and that’s what we were taught on. We were taught that sample size is always going to be a zero to two, right? Yeah. But the black girl sample size, at least at minimum, skinny black girl size is going to be a six, but they’re going to be a six at the top and probably eight at the bottom.
We go through that all the time at work. It’s like, Everybody here is a black woman. Please put, booty room.
Tish, that’s your expertise. You develop stuff depending on the company.
Yes, I develop the grades, the sizing, initially all of their spec, and then we send those specs over to a pattern maker and they will make the pattern, cut the garment out, and we will get the sample back to try it on a fit model. Once we try on a fit model, that’s when I’m making corrections and telling the factory or whoever made the pattern how to correct it. But also now using 3D, Browseware and clothes avatars to stop a lot of samples being made because that cost waste. So it’s more of a sustainability thing. However, I got into it because literally I love computer pattern making. It was a surprise and all the mess. Surprisingly, I didn’t have to draw.
That got you out of drawing stuff.
As long as it didn’t involve drawing, you were good.
But if somebody wanted to do what you’re doing, how would you suggest them getting started?
I would say one, if you don’t want to go to school, look up keeping you in stitches. My website would be on the great. Shameless plug.
No, non-shameless plug.
That’s right.
Non-shameless plug. Exactly.
But you can also get into the industry by becoming a tech design assistant. However, I will say one thing you, a tech designer, you need to know sewing and pattern making. I know tech designers and people that have years under them and they do not know pattern making. It completely confuses me because I’m like, How can you actually look at a pattern and tell the factory how to make it if you don’t know pattern making? You still have to know how to do it in order to tell them how to correct and know when they are doing it correct.
Even if you have a really good pattern maker, when you get it back, you have to know what you’re looking at or you’re going to waste a whole bunch of muslin, create these samples, and they’re all going to be wrong because you didn’t know that the bus dart should only be two and a half inches. They should not create a bullet there.
Right. Madonna in the ’80s.
Exactly. Also, you need to know how to do patterns because sometimes, and this happens a lot in the industry, you will tell them to do something, they’ll send something back, it will look okay, then for some reason, maybe between the first and second count sample or PP, it will be something completely different. And it’ll wind up in stores looking completely crazy.
And tell the newbies what PP is.
Okay, so there are stages of samples, like a counter sample, that would be your first time looking at it, second counter sample. A PP sample is pre-production. This means right before they go into production, this is your sample, and it’s going to be an actual fabric with actual trim. You’re trying it on a fit model. You want to make sure that you are proving everything on this sample. It should literally resemble what is going to hit the stores. And it should be flawless. And it should be flawless. And it should also come with the pattern.
The crazy thing about is, just from years of experience, even when you see the PP, if you don’t have quality control in the production process, sometimes you come back with stuff that looks totally off. The grading is off, the trim is off, the sewing is off. So if you’re going to produce a lot of garments, you have to have quality control built into the production process. So it’s not just that. You can’t just let it go and trust the factory. You can’t trust the factory. You’ve been dealing with them a while and-.
Like Tish said, you got to research these factories because some of these factories are sitting in a call center scamming.
If you haven’t been over there and see for yourself that it’s an actual factory. They do have domestic factories where you can visit, but the pricing is like- Yeah.
USAa pricing.
I would also say in that, talk to people in the industry. Ask them who they use. You have an expert on this podcast. Hit her up and say, Hey, do you know a good factory that can help me make athleisure? Or, Do you know a good factory that does denim? Each factory could make everything, but you want the person that does the best in that thing.
Exactly. They know how to deal with knit or woven.
Just because they say they can do denim doesn’t mean they can do denim. They’re going to say they can do whatever you want because they want to get paid.
Exactly. Because they want to get paid. And as a tech designer, generally when customers go to the store and they return samples, and it’s because they may complain that it may be the sample was dyed, maybe a dark blue, and it actually rubbed off on your sofa, but there was no sign on the pair of hands. I can tell you, hey, the dye is going to transfer, or if it shrinks seven sizes, or if something happens to it and you return it, it comes back to that technical design. Whoever made it, it comes back to them and to the factory. So someone has to take responsibility for that.
It’s so funny because people always laugh at me because I wash every new thing that I buy before I wear, everything before I wear it. I want to know if it’s going to shrink. I want to get all the color out of those jeans. People are gross. I’ve worked in retail long enough to know that people are disgusting. If you get a sample, ask them to send you a piece of whatever material they’re using, and take that material and wash it. See if that sample shrinks. See if that dye runs and when it dries, wash it again to see if it’s still running and if it’s a problem with the dye. It’s so much that goes into that technical aspect of it.
I’ll give you two examples. One of when we talk about when you buy clothing, this is a prime example of why, must, and all the cause. You must wash everything that you purchase. Don’t just take it and put it on. Because there was a dress and you walk and look this up, we’re actually probably will show a little clip of this article. A woman bought a dress. When she bought the dress, she put it on because she did not wash it. And when she put it on, she got scratches on her leg because there was a mouse foot sewn into the hem of her dress.
Oh, my God.
Yeah, we’re not going to put that link to that video. We don’t need it. No one wants to see that. No one wants to see that.
I mean, not the video, the article.
No one wants to read it either. And then just on the retail side, I’ve worked in a couple of retail establishments that shall not be named. They took back underwear and bathing suits.
Didn’t do anything. Just put it back on the shelf.
Yes. It’s just astounding to me. I bought some sneakers and the lady said, We can just bring them back. I mean, if you wear them, we’ll take them back. We’ll just recycle them. Again, it was at a major sneaker store, not even the outlet. This is a major sneaker store. I was like, What? I am confusion. We know a major department store will take anything back.
What do they do with the stuff after people return it and they’ve been worn? Do they just put it back out?
Allegedly. Yeah. They recycle it.
Let’s learn to wash your clothes when you buy it.
Tish, do you do consults? Like if somebody was to call you up, do you charge for consults or what’s that?
I do consults generally the first 15 minutes is a free consult. But yes, I do do consult because I think it’s good to talk to factories and talk to corporations just to see what the scope of their project that they need, and for me to pinpoint where I can help them and what all of their needs are. But yes, I do do consult.
If somebody wanted to do what you do, you don’t necessarily have to go to school, but you have to know pattern making and sewing, like how to put a garment together. You can learn that how.
Someone on this call teaches sewing.
Naima teaches sewing, yes.
I teach the sewing, the flat pattern making, draping, everything. Pretty much everything that you would learn at a college university, I teach.
How would somebody put a portfolio together for that?
With tech design, it’s a bit different. Our portfolios generally consist of showing how a garment looks on a dress form. Let’s say the dress form behind you. We would have samples of different types of garments on our forms, and we would show how we are telling the factory to make it. That could be in pictures and in pattern corrections. We’re actually doing a flat sketch of how they can correct it on the pattern and also showing what the measurements are and what we need them to change them to. You’re showing them how to actually change and correct this style. It’s more of a log of the different type of garments that you’ve worked on and how you go about telling corrections.
Right, and your process.
They do that because there are a lot of people that would go into tech that do not know pattern making, and then when they get in, they don’t actually know how to do the job effectively.
Any last words on keeping me in stitches?
As I said, I am a tech design, so if you are like me and you can’t actually do or you’re not all that wonderful, there’s another route in the fashion industry, tech design. And now that we have Browseware, which is 3D tech design, those are avatars. Now it’s beginning to be a lot more tech. So you can also do everything digital. Oh, that’s true. Which gives you a leg up, because now you can actually work to become fully remote.
Do you teach any of the digital programs? Do you teach Browseware?
I am getting ready to start recording videos for Browseware and Club. Cool. Yes, because I am certified in Browseware, so I’m getting ready to go back and do videos for that.
Very nice. So there will be a course on the Browseware and how to apply it to-
Yes, there will be a course on Browseware. But that comes after because in order to know Browseware, you need to know, in my opinion, it would make it easier if you knew illustrator because we have the same precepts. And also you need to know how to sew before you get to Browseware. You need to know a bit of pattern making.
Or just garment construction in general, how to put it together, a garment. You might not have to be good at sewing, but you have to know how to.
Put the pieces together. You just know how to sew it.
That’s keeping you in stitches. If you wanted to know any more about what Tish does, just go to her website, keeping you in stitches, or follow her on Instagram or Facebook or any of the socials.
All the socials.
If you have any questions about what she does, just hit us up on design, designers, plants, and coffee. All right, Tish, you can take us out.
All right. That’s all for us from designers, plants, and coffee. I’m Leticia Winston of Keeping You on Stitches, along with Zahiyya of Region Design Agency, Naima Dozer of Fearless Threads. See you next time.
And also Cover Me Chic.
That’s right.
All right, thank you.
We’ll see you next time.
We’ll see you.
Next time.
Subscribe to our newsletter with stories from our experience in the fashion industry and the best design tips.
We publish bi-weekly on Friday’s at 7am.